Как выбрать идеальную мебель для своей квартиры? Ответы здесь!
Артис-мебель: новости мира мебели
Мультифабрика «ШКОМ» преподносит подарок дизайнерам
Идея родом из детства
Натуральное дерево становится всё более дефицитным и дорогостоящим материалом. Условия его использования напрямую зависят от изменчивых характеристик древесных пород. Физико-механические показатели древесины весьма нестабильны: анизотропность («неравносвойственность»), гигроскопичность (поглощение и накопление влаги), усушка, растрескивание и т.п. Не менее опасно влияние бактерий и грибков, разрушающих слоисто-волокнистую структуру уникального природного материала. Кроме того, массивная древесина – очень тяжелый материал. Всё это создает предпосылки для поиска новых технологий, которые позволяли бы получать новые материалы, у которых эти недостатки либо отсутствуют, либо проявляются в меньшей степени
В начале года специализированное издание «Мебельщик» (2005, №1) сообщило о буме так называемых «композитов», материалов, созданных на основе нескольких компонентов - «…в нашей стране, например, их потребление за последнее десятилетие выросло в десять раз» (с.53). Одной из наиболее интересных новаций в этом направлении стало изобретение мультифабрики «ШКОМ», получившее название «композитный декоративно-конструкционный брус», или «ЛАЙТБРУС». О нем рассказывает руководитель отдела технологий и экспериментальных разработок компании Александр Зайцев.
-«Лайтбрус» - название, как я понимаю, связанное с тем, что будет «легко создаваться, выстраиваться, являясь чем-то легким». Ваше изобретение ориентировано на архитекторов и дизайнеров?
-Да, в первую очередь композитный декоративно-конструкционный брус предназначен для них. Хотя, если ещё более обобщить, то можно сказать, что «Лайтбрус» предназначен для человека, который понимает красоту и практичность конструктивных изделий и сооружений, знает толк в современном дизайне помещений, качественном и модном.
-А что можно сделать из «Лайтбруса»?
-Как один из разработчиков этой новинки, я бы хотел воскликнуть - да всё что угодно! Но понимаю, что характеристику возможностей нашего изобретения в публикации надо чем-то ограничить… Ну давайте остановимся, к примеру, на выставочных стендах, интерьере офисов, необычном дизайне витрин, зонировании помещений, создании мебели в стиле модерн… Хотя, как Вы понимаете, каждый из названных блоков можно раскрыть и получится очень длинный список того, что можно сделать и уже, кстати, делается дизайнерами в плане эксперимента и теста. Насколько мне известно, они с энтузиазмом отзывались о нашей разработке. В интерьерах, где необходима имитация натурального бруса, изменение уровней полов и потолков, говорят, просто незаменимая вещь…
-В чем её особенность, расскажите, пожалуйста, подробнее.
-«Лайтбрус» - это очень легкий, не требующий таких массивных креплений, как натуральные балки, фанерно-пенополистироловый фанерованный шпоном брус. Недавно нам предложили аналогию с «сэндвич-панелями», используемыми при конструировании крыш и мебельных стенок. Но эта аналогия очень далекая.
«Лайтбрус» имеет внутренний технологический паз, в котором располагается либо проводка, либо крепление в виде металлического стержня-стяжки с резьбой, за счет которого его можно удлинять по мере необходимости. Наши стандартные конструкционные брусы 2,40 или 3,0 м могут быть сочленены, как звенья. Очень удобно.
-«Лайтбрус» сочленяется только через внутренние металлические стержни?
-Нет. Можно, при известных размерах, склеить отдельные композиции: вдоль, перпендикулярно, по диагонали – в зависимости от задачи. Можно скрепить конструкционные брусы шкантами, клеем, стальными стяжками. Кроме этого, все варианты сочетаются. Фрагменты, сочлененные шкантами, могут быть в развитии интерьерной или экспозиционной композиции соединены через стержни с резьбой. Такое соединение может быть применено при создании интерьера в помещении любой сложности.
-То, о чём Вы рассказываете, мне очень напоминает конструктор «Лего».
-И не случайно. То, что мы создали – это фактически те же кубики или конструктор, из которого можно сделать хоть дом, хоть шкаф, хоть помещение…
-Я понимаю, конечно, что все такие идеи – родом из детства. Но всё же, как родилась идея «Лайтбруса»?
-Да, наш «Лайтбрус», действительно, пришел к нам из детства с кубиками и конструкторами. Но на фабрике мы сначала делали мебель из подобных материалов. Витринные стеллажи, винные стойки и стойки для радиоаппаратуры. Разумеется, это были разнообразные модификации того, что сейчас стало конструкционным брусом – «Лайтбрусом».
-Наверное, и те модели тоже привлекли внимание?
-Привлекли. Но интерес был не таким пристальным, как последняя новинка. Год назад, в рамках «Строительной недели» в Сокольниках мы презентовали концепцию конструкционного бруса. Однако показывался брус как атрибут стенда. И не более. А ведь вариативных возможностей множество. Только изменение размеров чего стоит! «Лайтбрус» может быть очень стройным – 40Х40 мм, а может выглядеть и как настоящий брус или балка – 160Х160 мм. В композиционных решениях очень выгодно сочетать размеры и в связи с этим классифицировать «Лайтбрус» и на потолочные, и на стеновые и на половые конструкции. После презентации появились даже неординарные дизайнерские решения: деревенский стиль оформления интерьера, подразумевающий столб и расходящиеся от него укосины. По длине брус просто безразмерен. Это зависит только от помещения.
-Если бы не легкость «Лайтбруса», его можно было бы принять за натуральную древесину.
-Совершенно верно. Он и задуман как имитация древесной балки, бруса. Впрочем, цвета могут быть самыми разными. Шпон итальянских фабрик дает возможность создать около 2,5 тысяч цветовых оттенков. Кроме того, грунтованная со снятым ворсом поверхность «Лайтбруса», превосходно подготовлена для декоративных лакокрасочных покрытий ( тонированный лак, воднодисперсионные и латексные краски, декоративные и фактурные покрытия ).
-«Лайтбрус» - это композиционное изделие, и созданное к тому же из композитов. Интересно, а с какими материалами он сочетается лучше всего.
-Если иметь в виду не столько технологическую, сколько интерьерную часть Вашего вопроса, то я бы отметил фанерованные шпоном плиты, зеркала и стекло, особенное – матовое или криволинейное. Стекольное производство «ШКОМ» открывает здесь также огромное поле для экспериментирования. -Просто находка для дизайнера!
-Знаете, когда начала вырисовываться идея «Лайтбруса», конструкционного бруса – ходило такое название «Подарок дизайнеру». Изначально как бы закладывалось то, что мы делаем его для интерьерных архитекторов и дизайнеров.
-Вот мы говорим о том, что конструкционный брус очень легкий и это здорово. Но меня, признаюсь, это несколько смущает. Я с улыбкой вспоминаю слова известного художника Никаса Сафронова, который говорит, что хорошая вещь должна быть тяжелой…
-Хорошо. Такой пример приведу. Для тестирования нового продукта выбирались самые необычные средства. Конструкционный брус выдерживал не только вес человека, но и массу легкового автомобиля «Рено-Меган» с пятью пассажирами и даже тяжесть грузовика «Газель». Да это что! Когда мы тестировали этот необычный брус, то кидали его под дождь – оказалось, что влажность для него не враг (он набирает до 20%), оставляли на трескучих морозах – не трескался и не рассыхался. Древесный брус, несоизмеримо более тяжелый, дорогой сложный в работе – давно вышел бы из строя. Ах, да, чуть не забыл – брус практически не прогибается и не «пропеллерится», чем «грешит» натуральная древесина.
Недавно мы провели такие публичные испытания: на брус длиной 2,40 м, положенный, как доска лавки, встал грузный человек (около 150 кг). Задачей было первичное исследование прогибания материала. Выяснилось, что при такой длине и воздействии веса «Лайтбрус» провис всего на 5 миллиметров.
-«Лайтбрус» внутри полый?
-Нет – там пенополистирол. Именно он и обеспечивает брусу прочность (т.к. фанера приклеивается всей поверхностью ), звуконепроницаемость, гигроскопичность (влагоустойчивость), а также возможность очень плотно держать гвоздь или шуруп, в отличие от того же гипсокартона или ДСП, которые сильно крошатся. Наш брус откалиброван с точностью 0,1 мм – это тоже очень важно. Те, кто работал с настоящим брусом, прекрасно знают, что неровности – большая проблема массивного бруса. «Лайтбрус» в этом смысле выглядит ровным , как струна.
-Пенополистирол, фанера, краска, шпон, клеи, лаки – не вредно ли всё это для здоровья.
-Кажется, что это самый сильный аргумент «против» «Лайтбруса». Однако брус соответствует всем санитарно-гигиеническим требованиям. Абсолютно безвреден. Экологичен. Пожаробезопасен. Обладает естественным древесным запахом. Кроме этого, ещё и лес бережет, являясь альтернативой балок из массивной древесины.
Смотрите также:
Возможно, Артис-мебель: новости мира мебели и другие предметы мебели интересуют Вас потому, что Вы планируете обновление интерьера? Тогда вот Вам одна из наших полезных рекомендаций на случай ремонта:
Время работы: 10.00 - 20.00
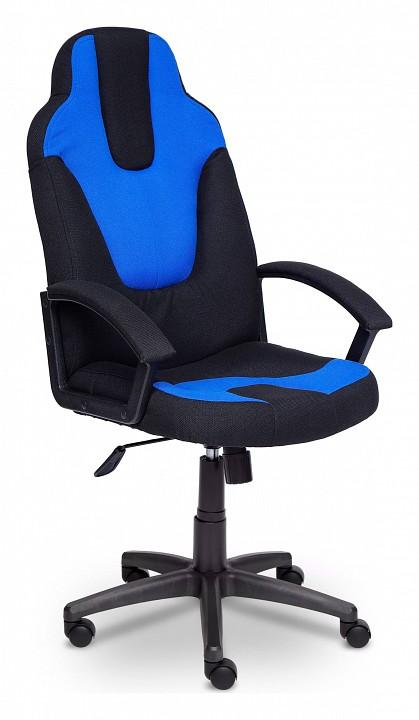
Tetchair: Кресло компьютерное NEO 3. Коллекция 2025 года.
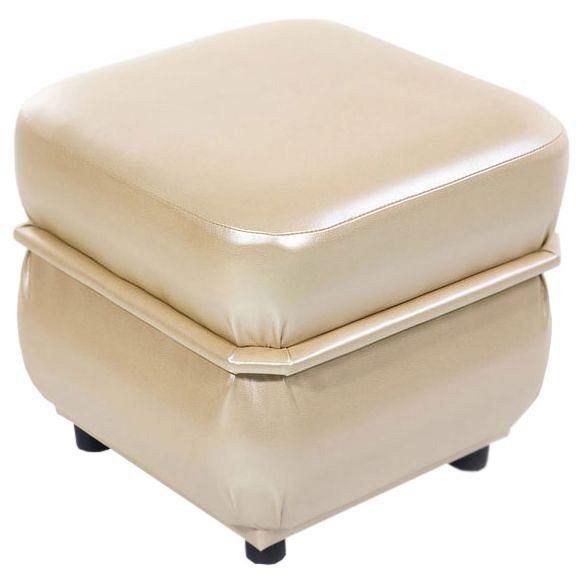
Бител: Пуф-сундук Призма. Коллекция 2025 года.
отзывы
Оставить отзыв (facebook):Оставить отзыв (ВКонтакте):