Как выбрать идеальную мебель для своей квартиры? Ответы здесь!
Артис-мебель: новости мира мебели
Бизнес на соломе
Производство строительных плит из отходов продукции сельского хозяйства позволит снизить объемы импорта древесины и обеспечить выпуск высококачественных строительных материалов внутри страны
Дмитрий Глумсков, "ЭКСПЕРТ"
Трудно предположить, что в ближайшие годы в мебельной промышленности может произойти технологическая революция. Мы привыкли окружать свой быт природными материалами - пластик отпугивает потребителей своими "неживыми" свойствами. Материал, способный заменить дерево, химики еще не придумали.
Последний прорыв в мебельном производстве совершили немцы в начале второй мировой войны. Вынужденные экономить на ресурсах, они изобрели технологию производства плит из отходов деревообработки. По физическим свойствам эти плиты не сильно отличались от цельной древесины, зато по цене значительно выигрывали. После победы страны-освободители по достоинству оценили экономную и очень удобную технологию. Уже к 60-м годам ДСП стал самым популярным материалом мебельной промышленности.
В 2004 году только Европа произвела более 40 млн кубометров древесно-стружечных плит. Главные достоинства ДСП - низкая стоимость и сравнительная простота обработки. Плиты делают из прессованной крупной древесной стружки с добавлением в качестве связующего вещества термореактивной синтетической смолы. Полноценным сырьем для ДСП является любая малоценная древесина как хвойных, так и лиственных пород. Причем европейские производители выдерживают пропорции - 80-90% хвойных пород и 10-20% лиственных. Мировой рынок торговли древесными плитами будет сдерживаться только дефицитом исходного материала. В определенном смысле он уже имеется, цены на древесину постоянно растут. Растут и объемы вырубки лесов.
Спасибо бюрократии
В этот устоявшийся за 50 лет рыночный порядок собирается ворваться казахстанский разработчик с заявлением, что его технология сделает ряд существующих способов производства ДСП невостребованными. "Дельта Форм" - название нового материала, существующего пока только в образцах площадью в несколько квадратных сантиметров. Это высокопрочные плитки из соломы. По мнению автора Виталия Хена, его технология перекрывает ряд недостатков популярных ДСП, ДВП: невлагоустойчивость, необходимость дополнительной обработки поверхности, возможность использования только в закрытой среде. Кроме того, эти плиты могут содержать в своем составе вредный для человека фенол.
История "Дельта Форм" началась в середине 80-х годов в Ленинградской лесотехнической академии, когда профессор Геннадий Царев нашел уникальное связующее для наполнителя - абсолютно безвредное органическое вещество.
Как известно, советская ДСП отличалась плохим качеством во многом из-за несоблюдения технологий по приготовлению наполнителя. Стружечные станки советского производства давали разнородную по форме стружку, импортное же оборудование быстро изнашивалось из-за варварского отношения к технике. Исходный материал плохо склеивался и расслаивался при прессовке.
Придуманное Царевым связующее несколько уменьшало проблему некачественной склейки разнородной стружки. На этой стадии к технологии подключился Виталий Хен. Договорились, что научной стороной занимается Царев, а административные вопросы решает молодой специалист из Казахстана. Вклинить рацпредложение в народное хозяйство СССР требовало недюжинной энергичности. Советским заводам по производству ДСП новое связующее не нужно было в принципе. Боялись процедуры утверждения новых ГОСТов, смены технологических циклов. Разработчики решили продвигать технологии обходным маневром под лозунгом "Расходы в доходы!".
"Я начал заниматься этой технологией в 1989 году, - вспоминает Виталий Хен. - Тогда разрешили частное предпринимательство, в стране был острый дефицит стройматериалов. Мы посчитали, что рентабельность производства нашего ДСП составляла где-то 800% при рыночной цене. Нужно было найти поставщиков сырья". Ориентировались изобретатели на леспромхозы. У них, как правило, остается большой процент отходов: ветки, кора, щепа. "Я ездил договариваться в Вологодскую область. Директор хозяйства сказал, что у них нет отходов, при том что видны огромные гниющие отвалы древесины. А он объясняет, мол, мы должны работать по безотходной технологии, поэтому все оставшееся сжигаем. Если вы начнете производить что-то из этого мусора, то меня уволят или посадят, - говорит Хен. - Аналогичная ситуация была и в других хозяйствах. Больше всего мне запомнился разговор с директором целлюлозно-картонного завода в Кызылорде. В качестве сырья завод использовал российскую древесину, отвалы древесные сжигались, дым стоял по всему городу. Предложил закупать у них мусор, а директор отвечает, я вам, буржуям, не дам зарабатывать на народной крови, так и продолжал травить город дымом".
Виталию Хену пришлось искать другое сырье. В лаборатории экспериментировали с соломой, но результаты были плохие: она при горячем давлении часто сгорала. Ученик Царева предложил поменять связующее и несколько изменить технологии приготовления древесных плит - апробировали на рисовой шелухе - материал получился по многим физическим параметрам лучше, чем ДСП. С этого момента Хен начал самостоятельное продвижение "соломенной технологии". В СССР отходы сельского хозяйства фактически не утилизировали.
"В моей технологии необходима солома с высоким содержанием клейковины - это может быть рисовая шала, стебли злаковых, хлопок, в общем, основные сельскохозяйственные культуры Казахстана, - говорит ученый, - и биокатализатор, который превращает разнородную перемолотую массу из соломы в единый состав. После технологического процесса структура материала отличается от структуры ДСП или ДВП".
Соломенная бомба
Материал одобрил консилиум специалистов. Технологию принимали в Академии наук, где "Дельта Форм" причислили к прорывной технологии. Среди испытателей "соломенной плиты" был доктор технических наук Николай Буктуков. "Этот материал в три раза прочнее известных на сегодняшний день ДСП, экологически чистый. Делается из отходов (солома, шелуха), пожаробезопасен. Горит, если только держать его над пламенем. Легкий, с хорошей тепло- и звукоизоляцией. Кроме того, он примерно в 2-3 раза дешевле, чем аналоги из ДСП и ДВП", - перечисляет преимущества "Дельта Форм" г-н Буктуков.
В Белоруссии, России и Украине производят ДСП и ДВП с повышенным содержанием химически активных смол для обеспечения надежной склейки древесного наполнителя. Чистые способы производства древесных плит (без фенола) в среднем на 60% дороже. Причем производство высококачественных смол является одной из составляющих цены материала. В "Дельта Форм" цена связующего определяется лишь доставкой с поля малоценного с точки зрения сельского хозяйства мусора. Впрочем, и сам наполнитель номинальной цены не имеет. Теперь об экологии. Кроме "чистых" потребительских свойств основа материала представляет собой быстро возобновляемое сырье - 1 год для полного цикла восстановления, что не скажешь о классических плитах, у них так или иначе в ход идет древесина, на созревание которой необходимо тридцать и более лет, причем восстанавливается только часть из промышленно освоенного сырья.
Новые физические свойства фактически древесного материала разработчик получил, нарушив классическую технологическую цепочку производства ДСП и ДВП.
"Промывка, просушка - несложные процедуры, нет дрожжевания, клея, простая технология размежевания, нет пропарки. Все процессы как бы проходят в одном цикле - при горячем давлении в закрытом контуре. В процессе обработки солома как бы наполовину сгорает, получается сверхуплотненная полузольная структура, которая в результате не боится влаги. Материал не разбухает, так как все волокно фактически сгорает", - объясняет Николай Буктуков. Он считает, что "Дельта Форм" можно использовать и в качестве кровли, и в качестве стен.
"Если использовать эту технологию, то 1 кв. метр жилья европейского качества будет стоить не более 100-150 долларов. Причем строить можно как одноэтажные, так и многоэтажные здания. Стены можно делать из "Дельта Форм" - наружная и внутренняя плита, между ними прокладывать строительную вату, расстояние между плитами 5-7 сантиметров. Сама плита очень гладкая, почти как стекло, что не требует особых затрат на отделку внутренних стен. Дом получится прочный, теплый, экологически чистый",- говорит он.
Есть у нового материала и технологическое превосходство. То, что не может дать в принципе ни ДСП, ни ДВП - эластичность исходного сырья. "Сама консистенция до обработки ведет себя как пластмасса - абсолютно гибкая, что позволяет штамповать из нее сразу готовые изделия любой формы: двери, оконные рамы, стулья, посуду. Можно делать даже одноразовую посуду толщиной 2 миллиметра", - объясняет Виталий Хен.
Маркетинговый прикид
Мебельная промышленность Казахстана полностью привязана к импорту стройматериалов из древесины. ДСП и ДВП закупают в России и Польше. По данным статистических органов России, российские деревообрабатывающие компании экспортировали в Казахстан в 2004 году 31356 кубометров ДСП. Свои плиты производить, по мнению многих мебельщиков, нерентабельно - сырье все равно придется завозить. Лишь 4% территории республики занято лесами, и только 1,8 % - промышленно пригодными. Завозится до 70% необходимой древесины. Это ставит местных производителей в невыгодное по сравнению с российскими мебельщиками положение. Отечественным мебельщикам приходится работать с более дорогим материалом из-за транспортных расходов, прибавьте еще и таможенную пошлину в 15%.
"Дельта Форм", по мнению Виталия Хена, способен полностью заместить импортные древесные плиты - они дешевле. Сырьевой базы для массового производства предостаточно. В Казахстане ежегодно выращивают около 15 млн тонн пшеницы. Соотношение стебля к зерну равно 3,5 к 1. Только на пшенице можно получать около 50 млн тонн соломы. Из одного кубометра готового сырья технология Хена позволяет получать около 100 кв. м материала толщиной в 10 миллиметров. Только пшеничное сырье обладает производственным потенциалом в 5 млрд кв. м продукции.
"Не нужно строить большие заводы, достаточно запустить мини-цехи с несколькими линиями производительностью в 30-50 тыс. кв. м в год. Отдельно запустить линии по плитам, дверям, по напольному покрытию. Одна линия стоит примерно 200-250 тысяч долларов с учетом небольшой переделки: в моей технологии несколько иная система прессования. Хотя если производить свое оборудование, изначально оно будет стоить дешевле, технические решения по оборудованию есть", - делает вывод изобретатель.
Образцы своего материала Виталий Хен готовил на разном оборудовании: в лаборатории ленинградской академии, на заводских станках, а также в домашних условиях с помощью паяльной лампы и самодельного пресса. Технология отработана. Правда, в промышленных масштабах "Дельта Форм" выпускать еще не приходилось, но автор уверен, что его продукт рано или поздно станет самым популярным материалом мебельной промышленности.
Дмитрий Глумсков, "ЭКСПЕРТ"
Смотрите также:
Возможно, Артис-мебель: новости мира мебели и другие предметы мебели интересуют Вас потому, что Вы планируете обновление интерьера? Тогда вот Вам одна из наших полезных рекомендаций на случай ремонта:
Время работы: 10.00 - 20.00
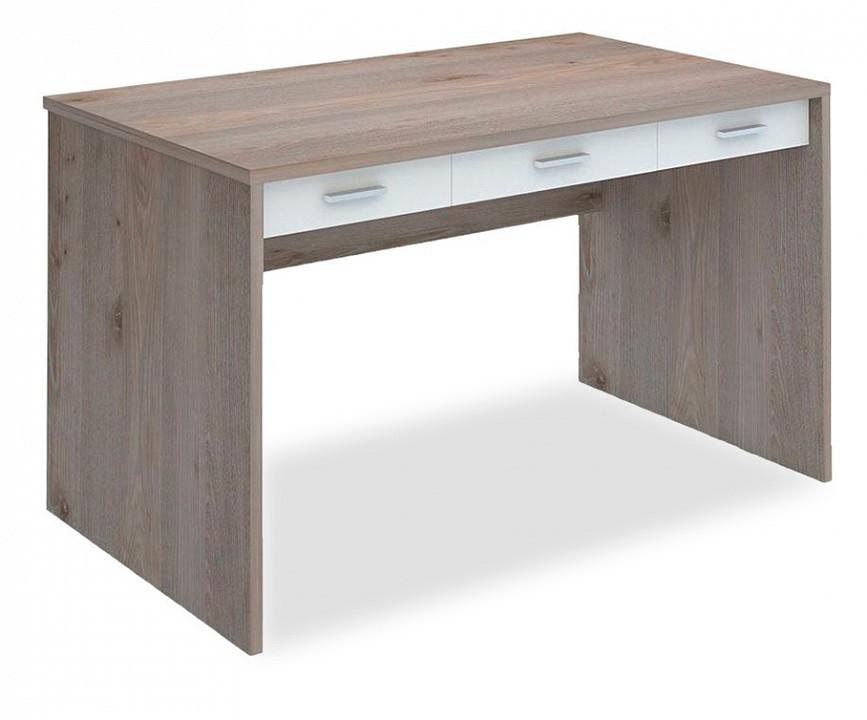
Merdes: Стол письменный Домино нельсон СП-82С. Коллекция 2025 года.
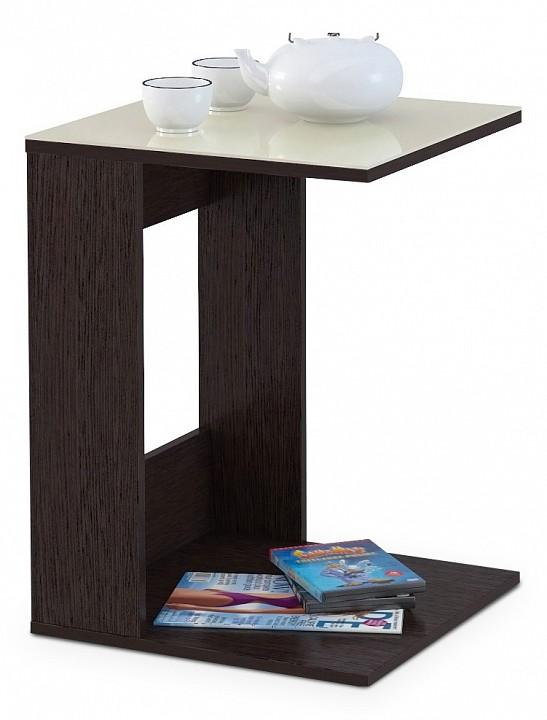
Мебелик: Стол придиванный BeautyStyle 3. Коллекция 2025 года.
отзывы
Оставить отзыв (facebook):Оставить отзыв (ВКонтакте):